The Gap Board Process
Gap Board was developed so that there would be some linear balance to the Nung and Klom series. The details of the Nung chair show that there were gaps between the bamboo strips, which was a design motif that I wanted to carry over to the board and panels. I worked with Graham Lamb, who is an amazing architect in Bangkok, Thailand on these dots and dashes. Graham developed a very complex system that had many different pieces that were built separately and then assembled. Sadly, this was cost prohibitive. In the end, the system I developed was a grid-like system of bamboo strips and then we randomly knocked out pieces, and colored them in a random pattern. It cost nearly $60/sqft less to do it this way and was much faster.
Gap Board was developed so that there would be some linear balance to the Nung and Klom series. The details of the Nung chair show that there were gaps between the bamboo strips, which was a design motif that I wanted to carry over to the board and panels. I worked with Graham Lamb, who is an amazing architect in Bangkok, Thailand on these dots and dashes. Graham developed a very complex system that had many different pieces that were built separately and then assembled. Sadly, this was cost prohibitive. In the end, the system I developed was a grid-like system of bamboo strips and then we randomly knocked out pieces, and colored them in a random pattern. It cost nearly $60/sqft less to do it this way and was much faster.
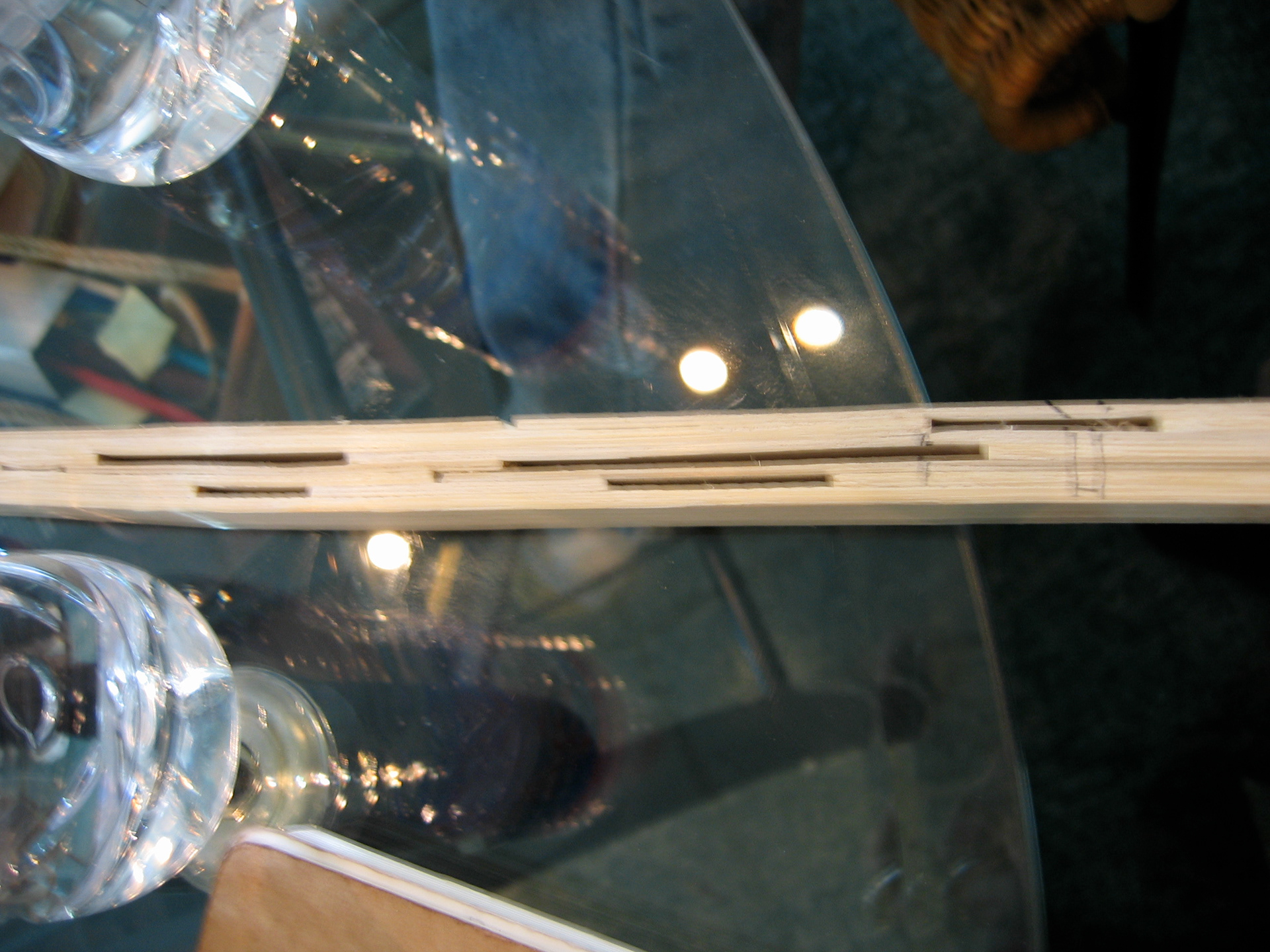
Not working yet

Try and try again... wrong glue, wrong pressure, wrong heat. Now we know...
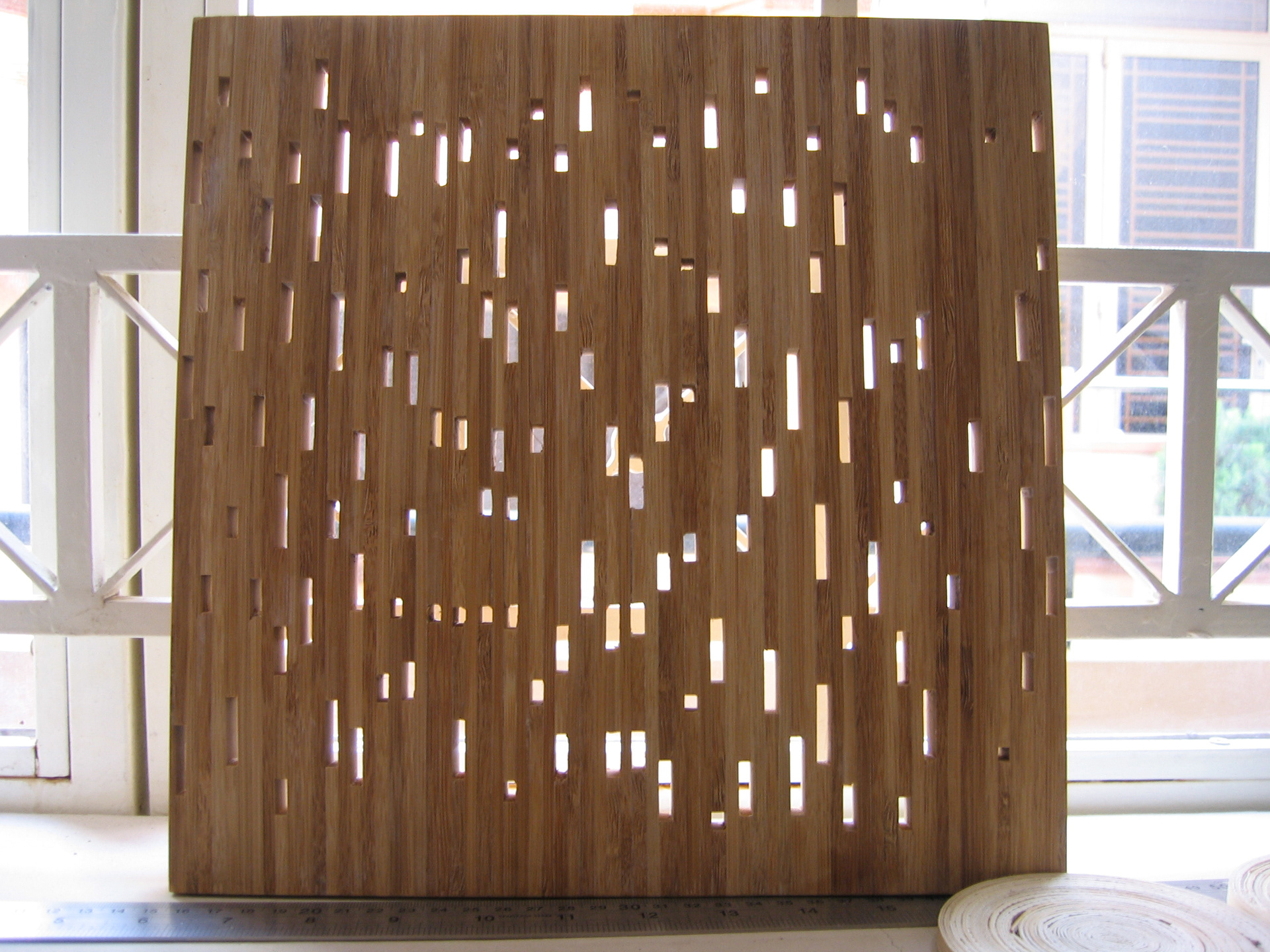
Structure is close but the gaps seem too small in a lot of ways and it begs the question: What kind of pattern are we going for? Random? Asymmetrical? Geometrical? You can see one of the unglued discs in the lower right that sparked the Nung chair
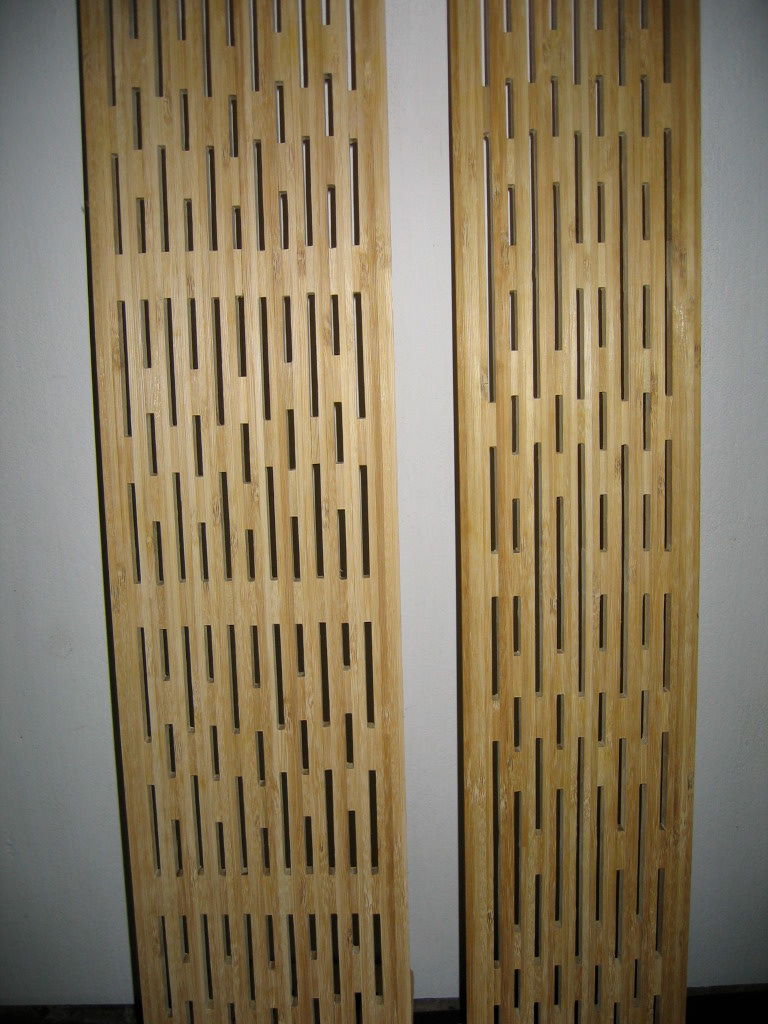
Unfilled gapboard, right after pressing and gluing

Color pattern sketch

Gap board with Coconut board
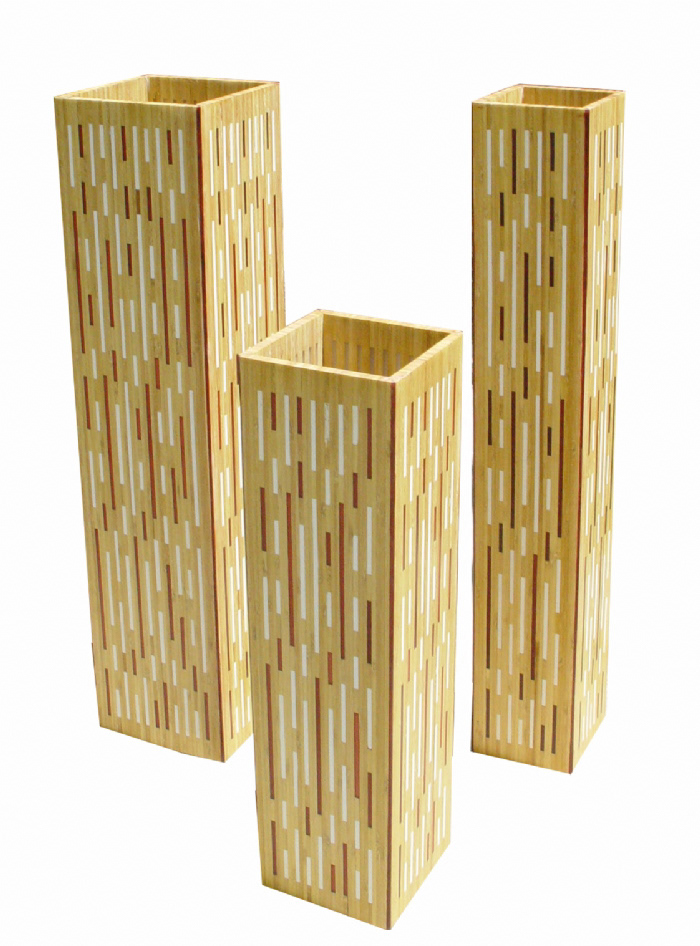
Gap Board columns/planters. These worked out quite well, but with one notable exception - the white resin was supposed to be translucent NOT opaque. Sigh. The refinement continues.
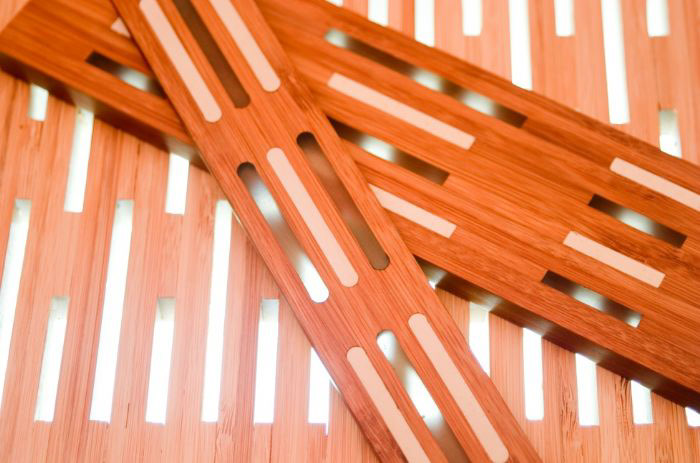
Honestly, my favorite piece of Gap Board. This is a different construction technique with was tested as a way to automate and simplify the process contrasted with the original technique. I love this shot. It is the most refined and pure that the product evolved to before we were forced to close Xeno Objects.
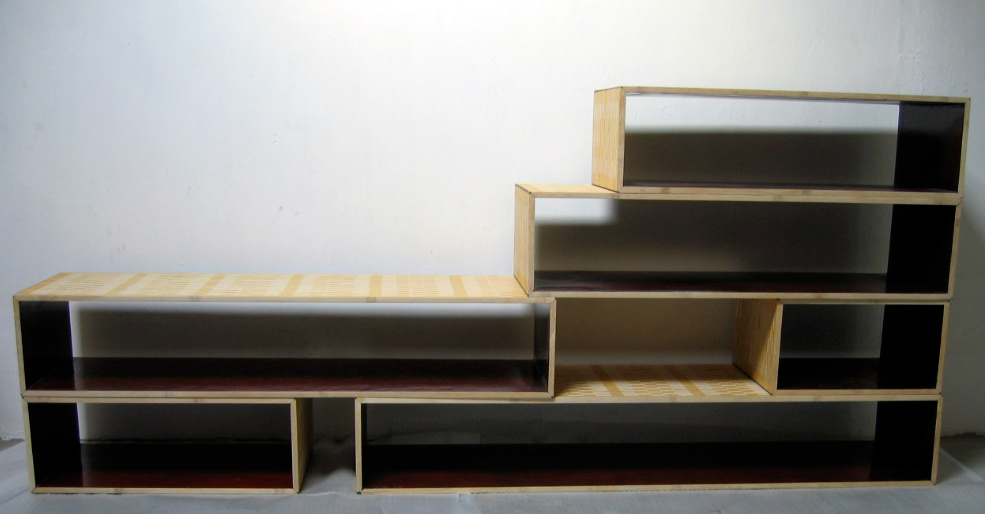
The ill fated cabinets. I never liked the proportions but that didn't mean they all had to commit suicide on the way to ICFF. None of them survived the trip.
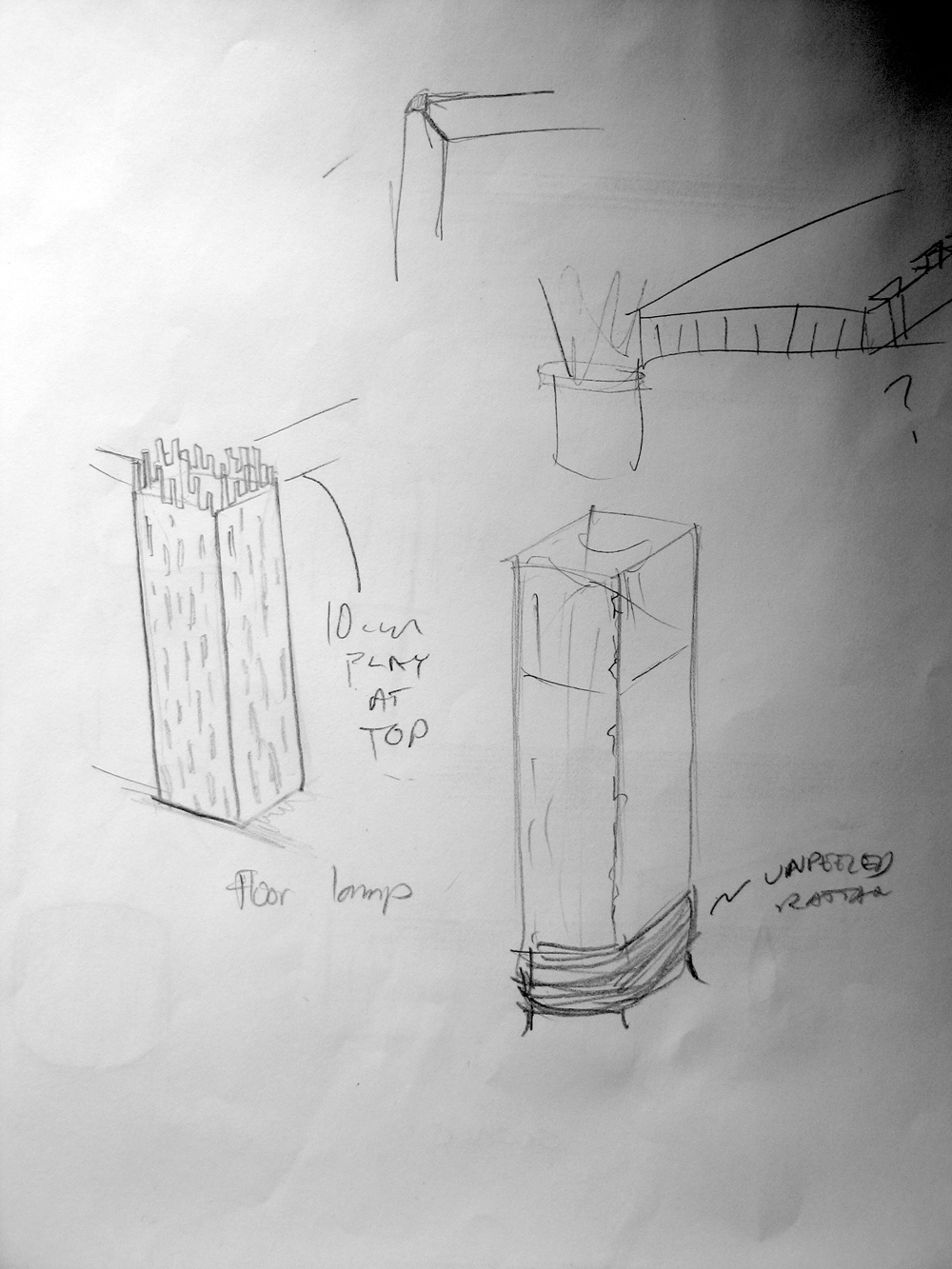
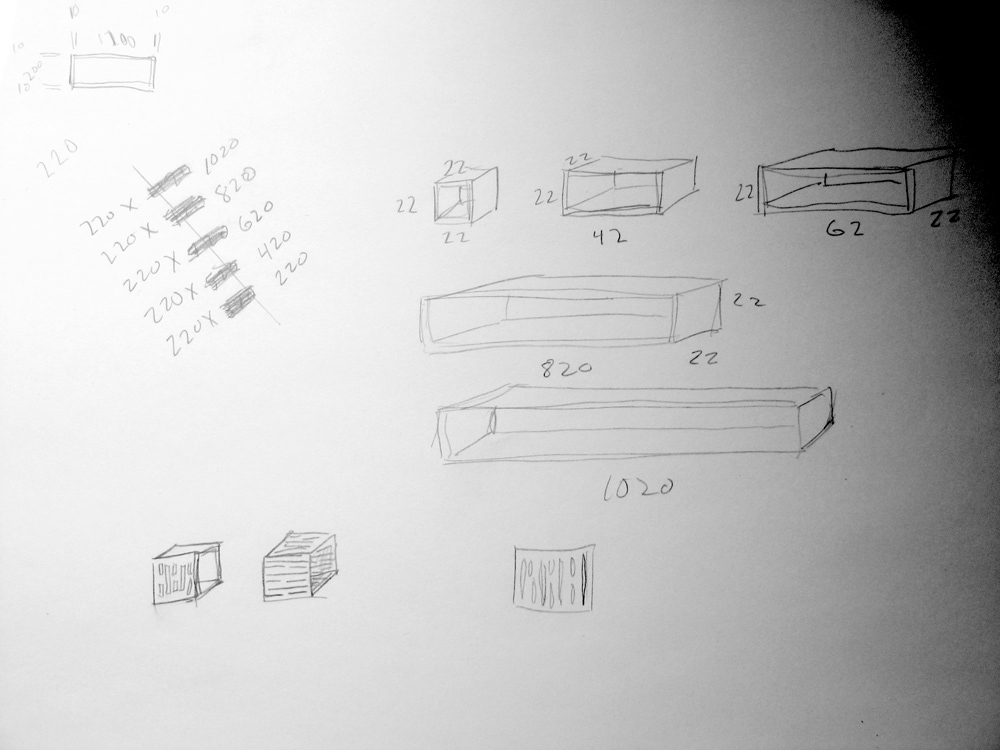
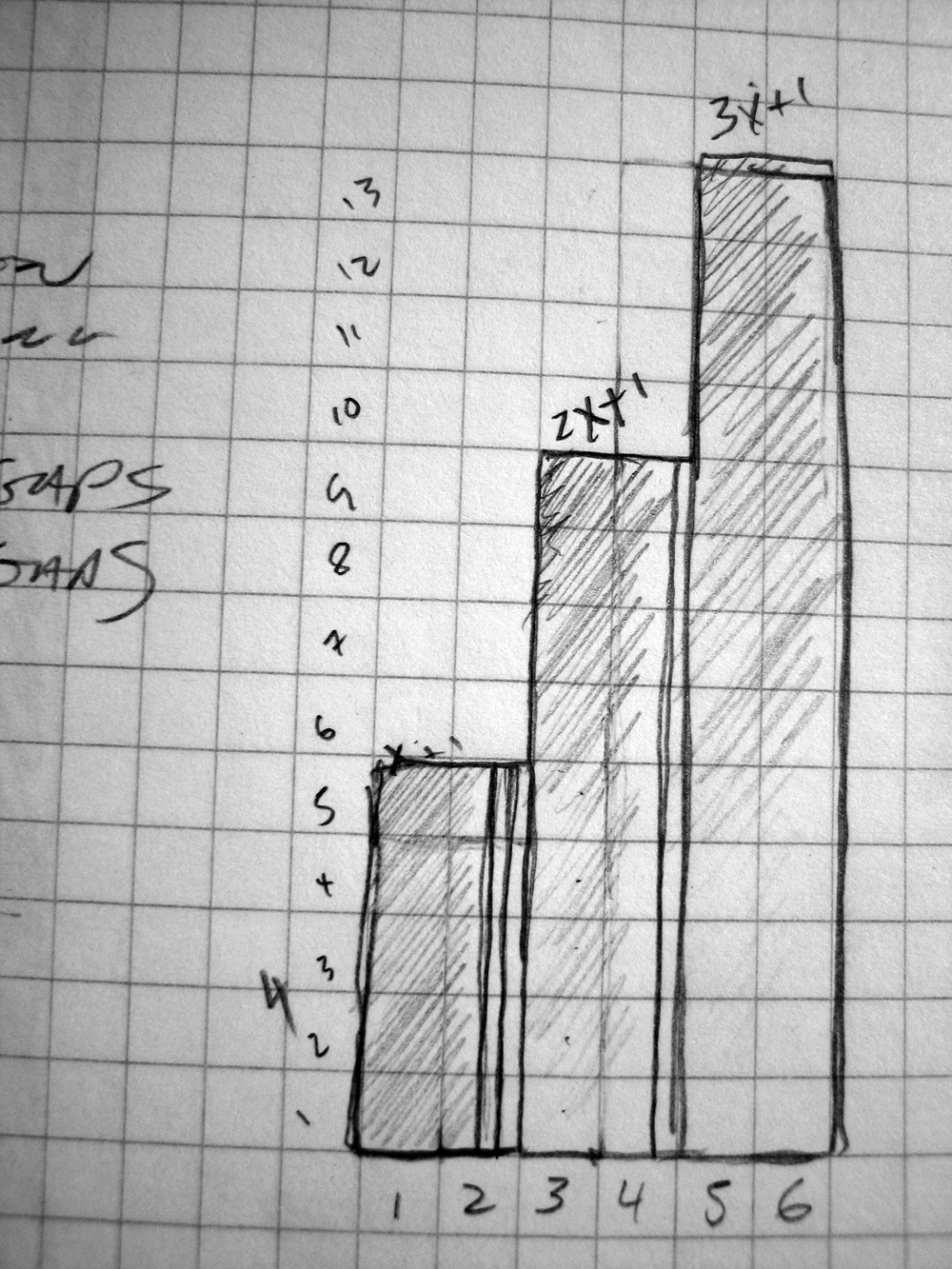
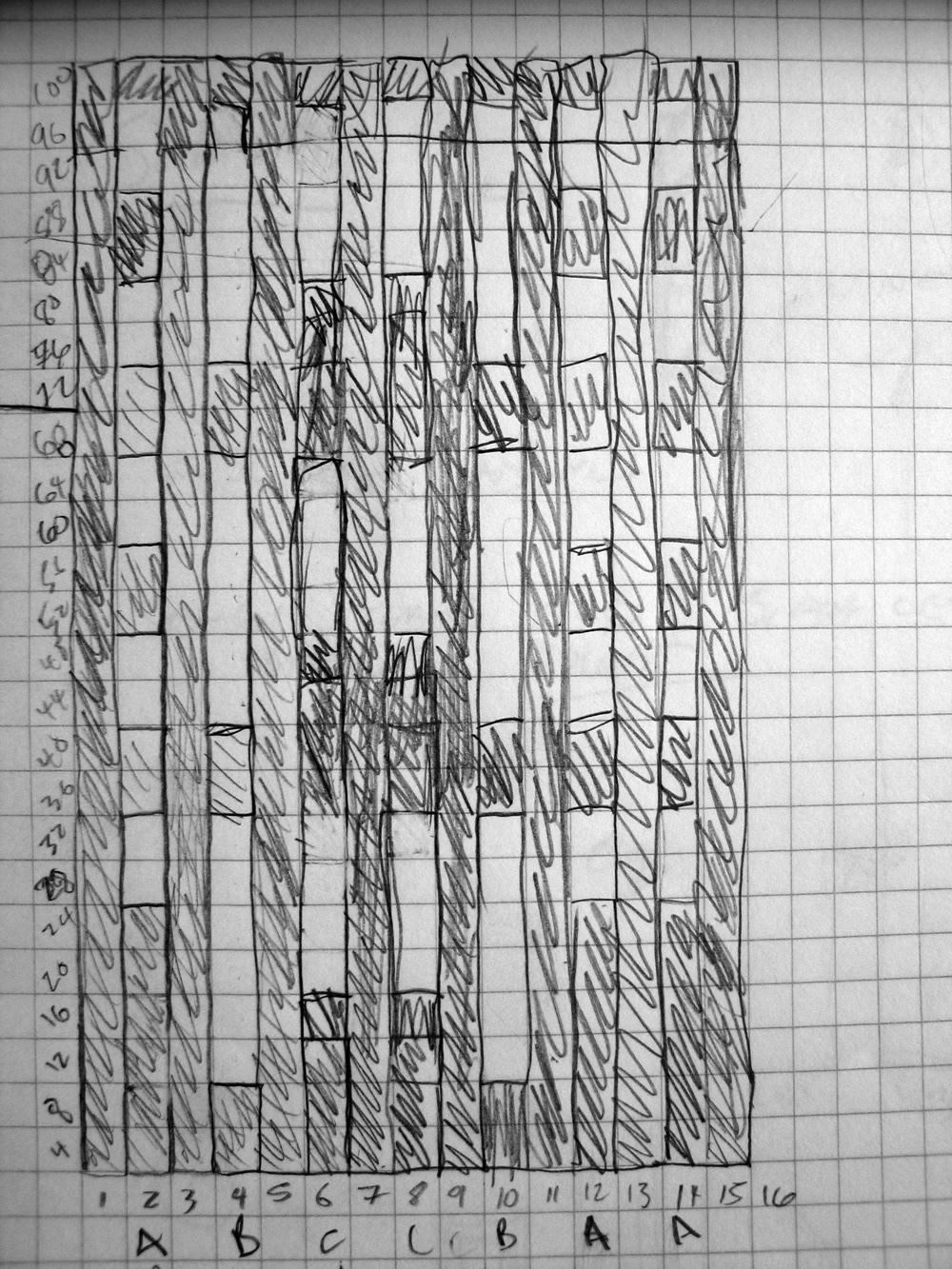
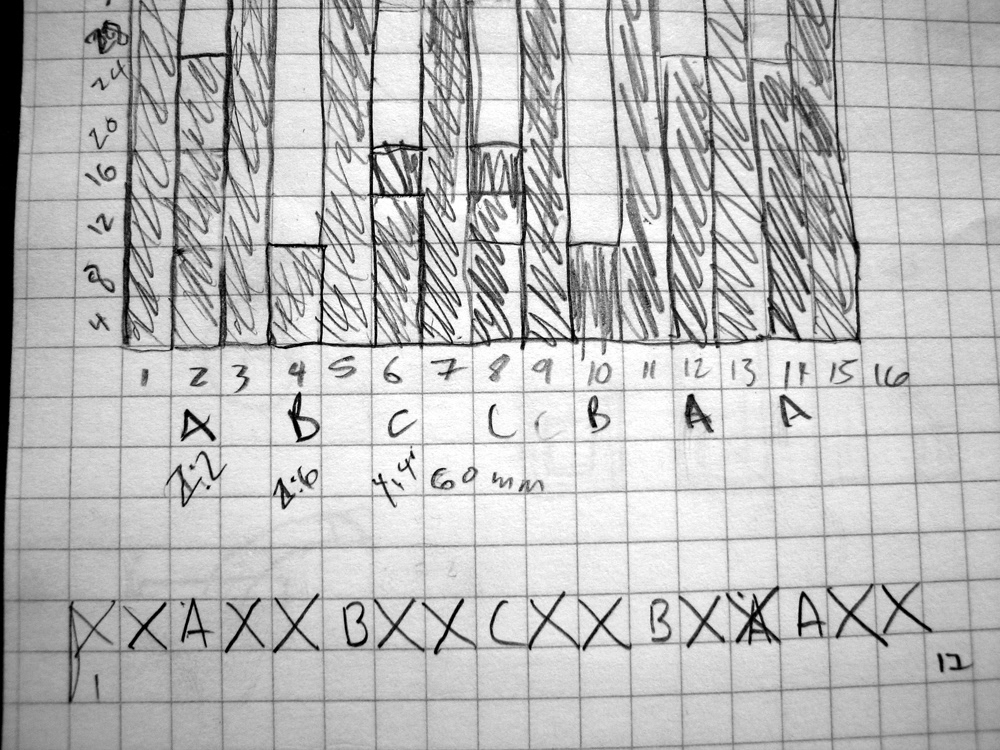
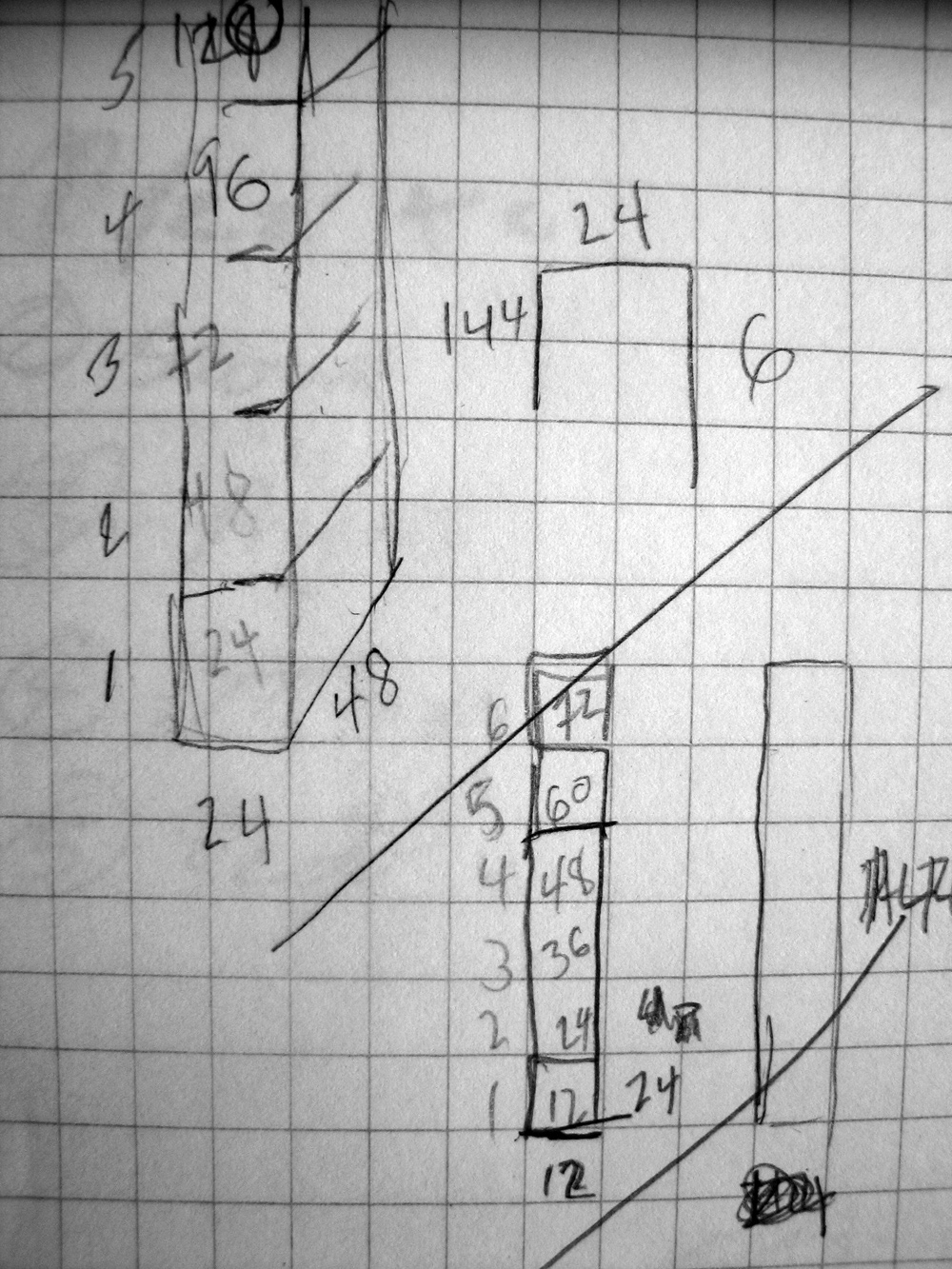
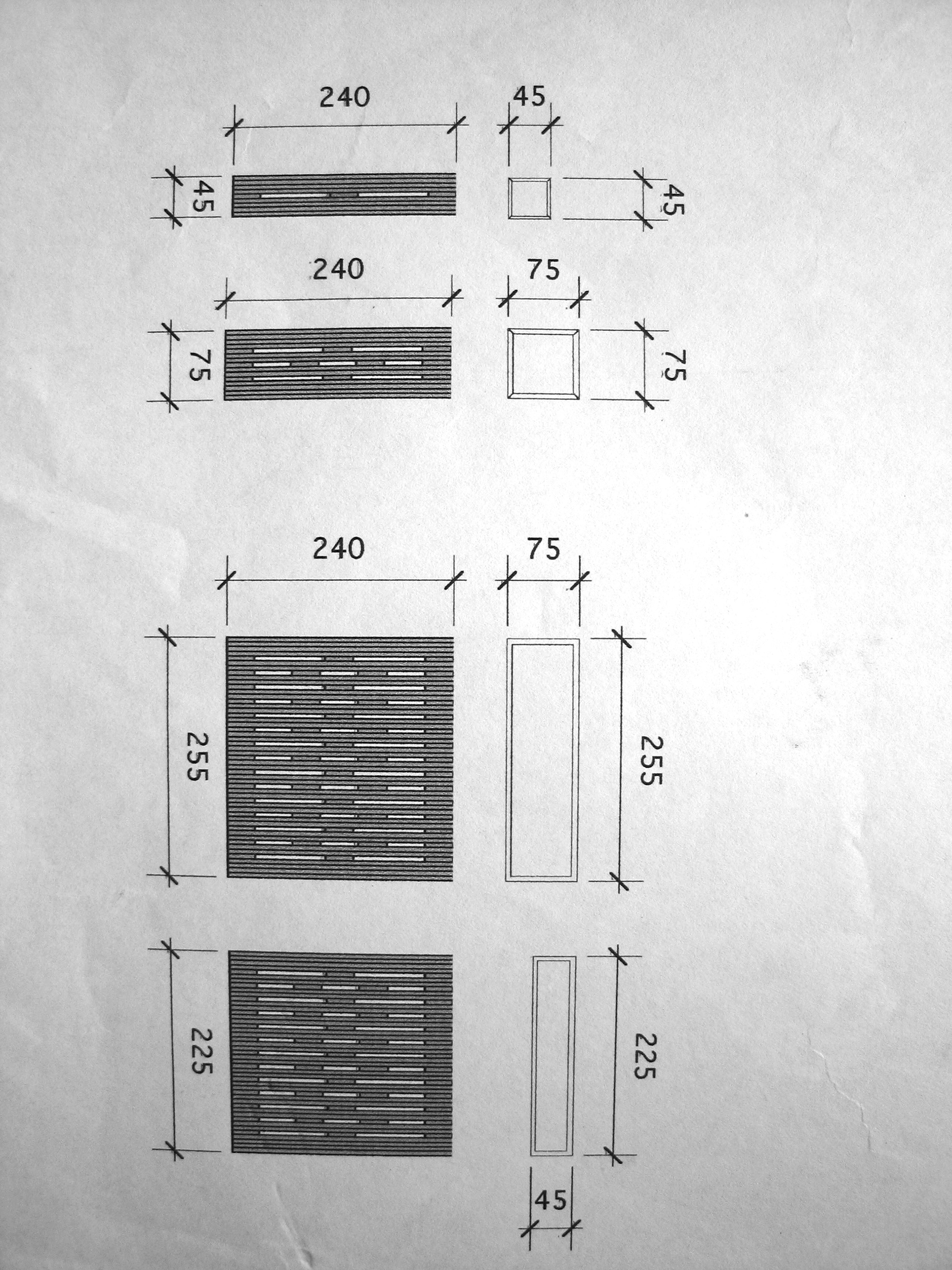
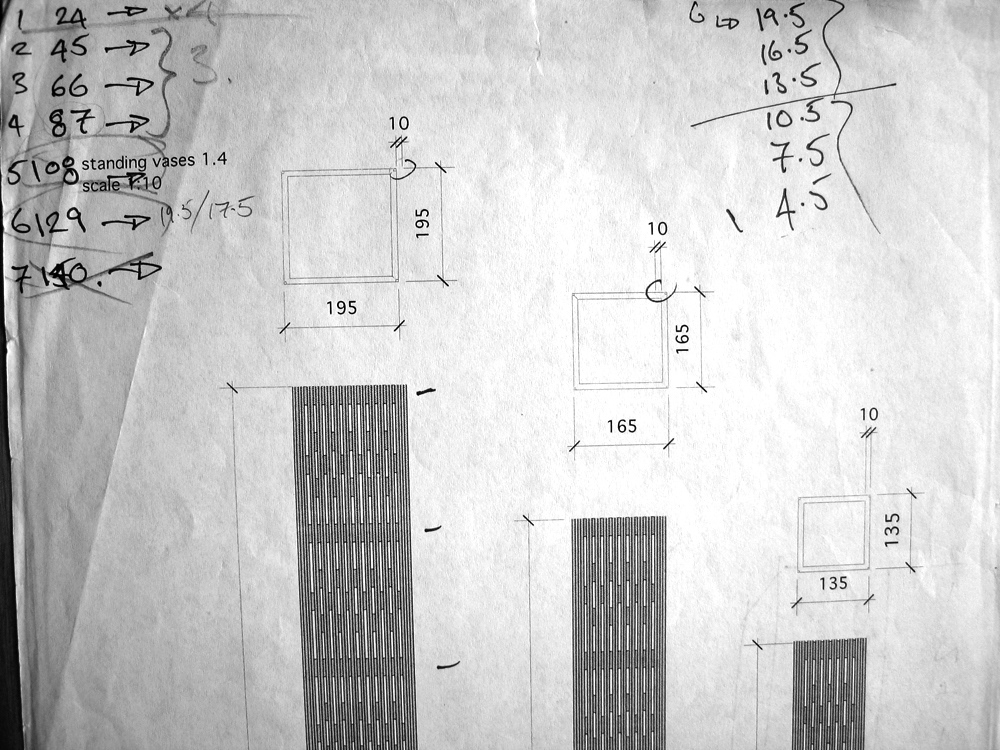
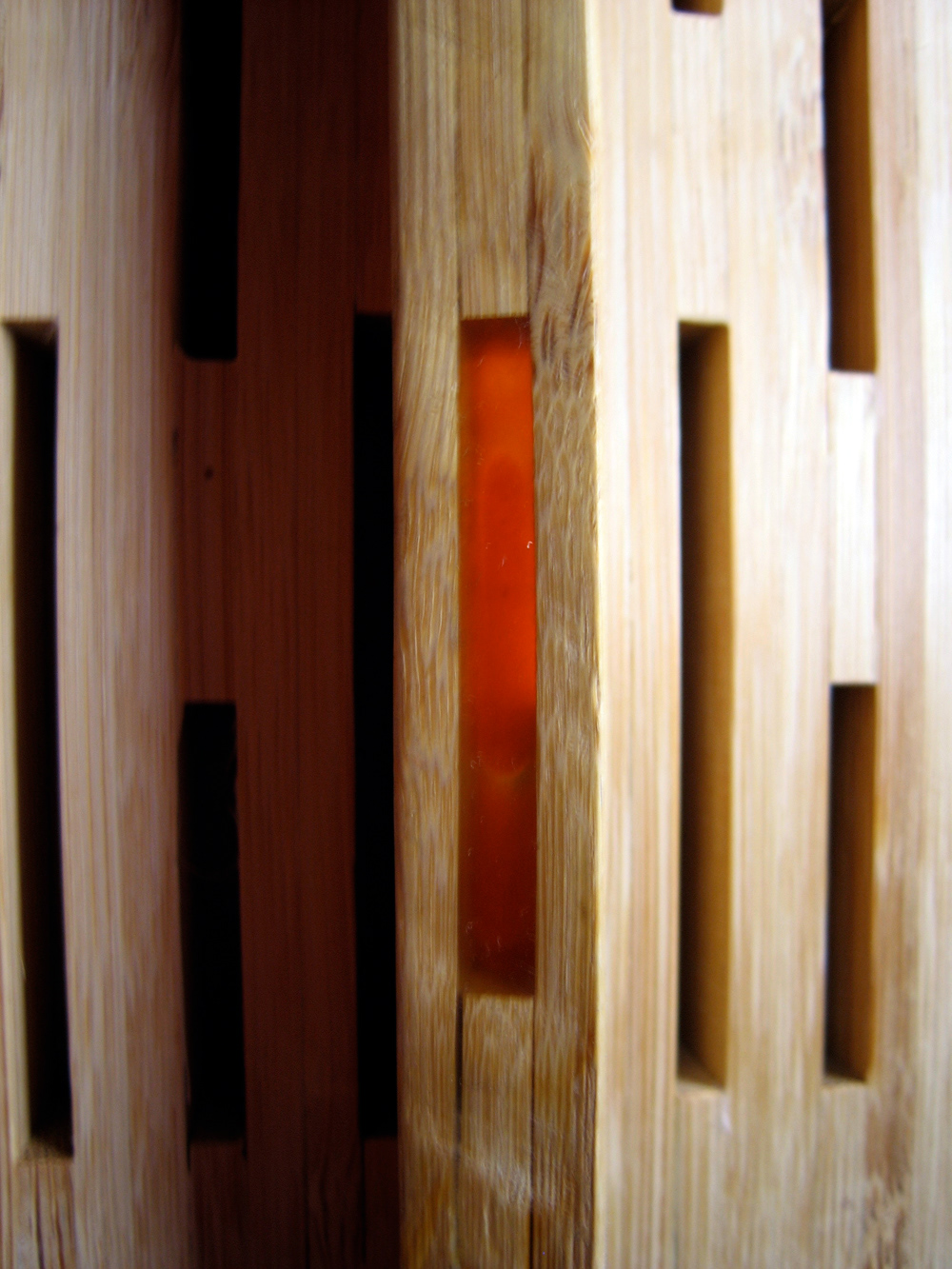
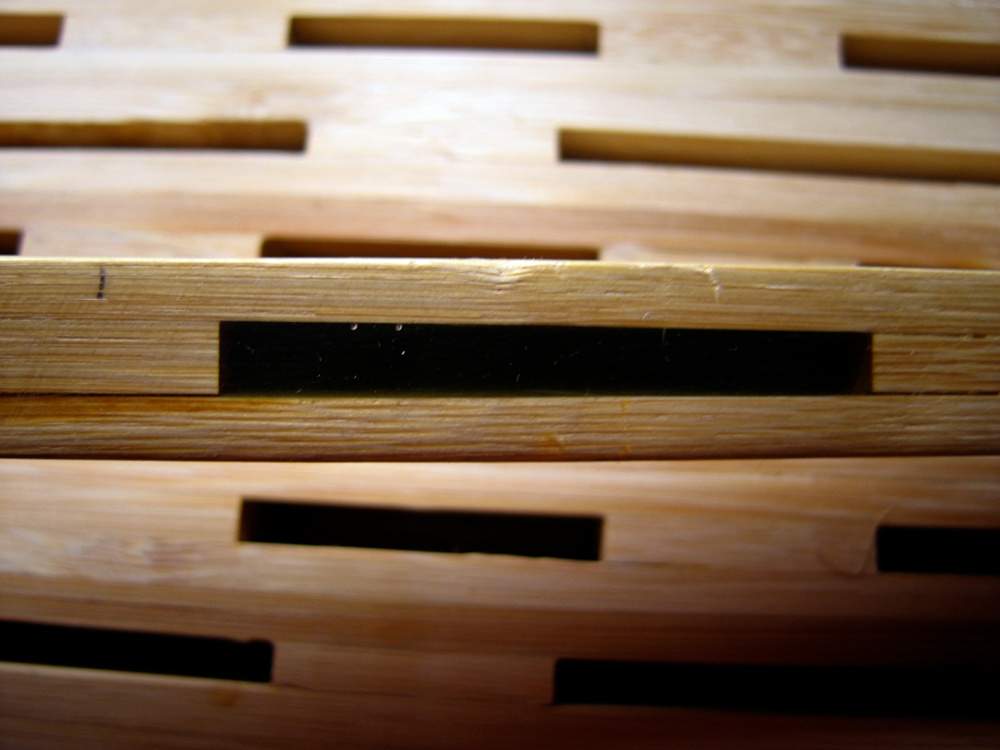
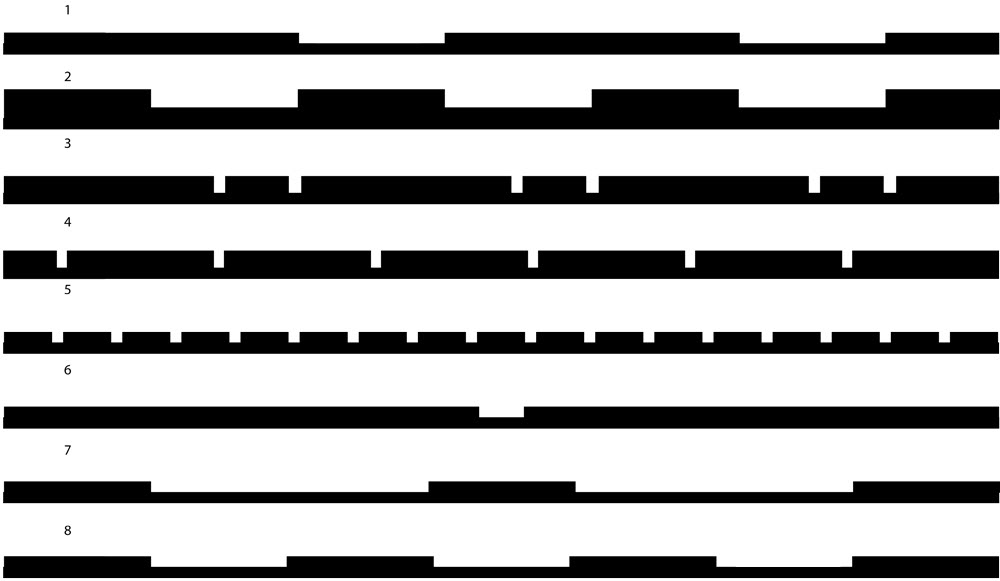
Graham's system. Wonderful but too complex for mass production. The final motif for Gap Board had only one unit type.